rotary drum granulator
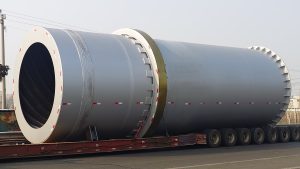
The rotary drum granulator is a granulation equipment widely used in fertilizer, feed, mining and other industries. It is mainly used to form powdered materials into granules by rotation. Its core components include an inclined rotating cylinder, a feeding device, a transmission device and a discharge port. During operation, the powdered material enters the cylinder through the feeding device, and gradually forms granules by means of rolling, friction and the action of an external binder during the rotation process. Under the action of gravity and centrifugal force, the formed granules move along the cylinder wall to the discharge port and are discharged. The rotary drum granulator has the advantages of high granulation efficiency, high granulation rate, low energy consumption, simple operation and convenient maintenance, and is suitable for the granulation needs of a variety of materials. According to different process requirements, the speed, inclination and cylinder lining of the rotary drum granulator can be adjusted to achieve the best granulation effect.
WE NOT ONLY PROVIDE RELIABLE PRODUCTS, BUT MORE IMPORTANTLY WE PROVIDE RELIABLE PROCESS DESIGN AND EXPERIMENTATION
Benefits of the Granulation Drum in Granular Fertilizer Production
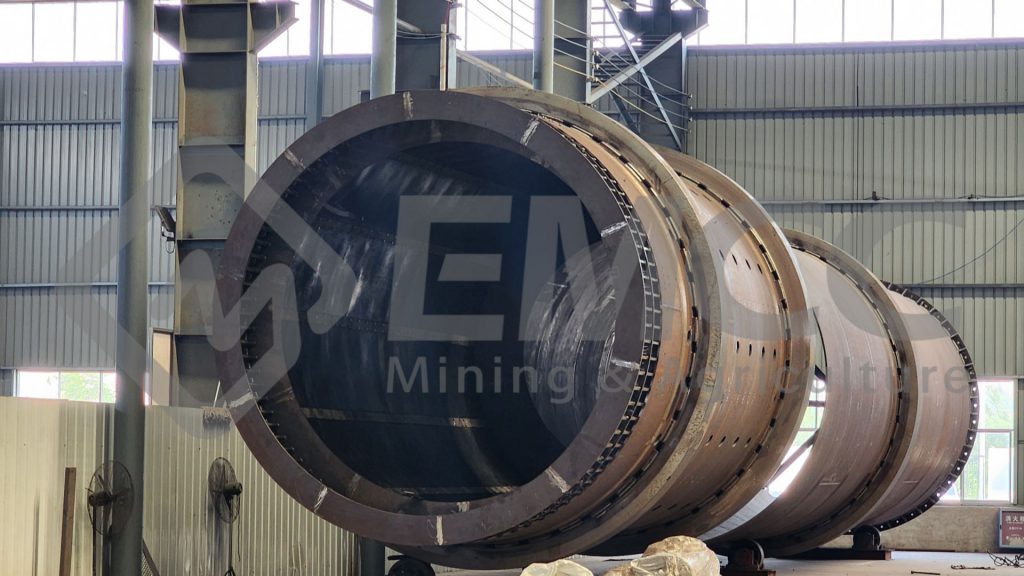
HOW THE GRANULATION DRUM PRODUCES A SUPERIOR FERTILIZER PRODUCT
The definition of a granule, as it relates to this piece of equipment, is a solid, spherical pellet, in the size range of approximately 1-6 mm. These granules can vary in physical properties and chemical makeup, depending on what is desired for the application. A granulation drum is frequently used to agglomerate inorganic fertilizers such as NPK; the nitrogen (N), phosphate (P), and potash (K) typically start as a fine powder, which can either be granulated into an all-in-one product known as a complex fertilizer, or granulated separately and blended together later to achieve the desired nutrient formulation. Without granulation, the fine powdery materials would be dusty and difficult to handle; the denser particles would settle to the bottom of the bag or barrel, creating an inconsistent blend (segregation) and causing significant application challenges. Similarly in the production of diammonium phosphate (DAP) or monoammonium phosphate (MAP), the granulation drum is utilized for a continued chemical reaction in correlation with the formation of a solid granule. The reaction, traditionally initiated in a pre-neutralizer tank, neutralizes the phosphoric acid slurry with ammonia, while simultaneously creating a granule that contains both phosphate and nitrogen. In addition to developing durable, consistent granules, the granulation drum can also create a more dynamic granular product. Different liquid binders and coatings can be used to create granules with time-release properties, or a multi-layered pellet can be created by adding different minerals at varying stages of the granulation process.GRANULATION DRUM DESIGN
A rotary granulation drum is relatively simple in design – raw material is fed into a large rotating cylinder, liquid binder is added, and the material tumbles to create solid, spherical pellets, in some cases utilizing a chemical reaction as part of the process. However, extensive design and engineering is needed in order to build a quality piece of equipment capable of creating a consistent product at high capacities. Several questions must first be addressed before granulation drum design can begin, some of which include:- Is the material(s) organic or inorganic?
- What is the nutrient content?
- What binders will work the best for the desired time release, while still preventing degradation from storage and shipping?
ADVANCES IN GRANULATION DRUM DESIGN
Nearly all industries have seen tremendous advancements due to modern technology. Some of the key advancements in granulation drum design include: Flexible and Corrosion-Resistant Drum Liners: Liners can be used to reduce or eliminate material build-up on the drum walls, as well as decrease the potential for damage caused by corrosive materials. Tumbler flights: Tumbling flights can be used to increase the material agitation in order to perfect the cascading effect and create the desired granule properties.CONCLUSION
The granulation drum has long served as the basis of modern fertilizer production. This versatile piece of equipment has helped bring numerous fertilizer products to the consumer market by creating a durable granule that is easy to handle, package, ship, and apply. EMCC has been the preferred supplier of granulation drums to the fertilizer industry for over 10 years. Our granulation drums are rugged, reliable, and manufactured to the highest quality standards. We also offer unparalleled feasibility testing and granulation process development services in our testing facilities, as well as comprehensive parts and service support. To learn more about our granulation drums or services, contact us today!WE NOT ONLY PROVIDE RELIABLE PRODUCTS, BUT MORE IMPORTANTLY WE PROVIDE RELIABLE PROCESS DESIGN AND EXPERIMENTATION
Testing Crucial in Granulation Drum (Granulator) Design
Granulation drums are utilized in many industries, processing a wide range of materials into a more usable, more marketable granular form, whether it be for use as a fertilizer, chemical agent, mineral, or otherwise.
Since all materials respond differently to granulation, the design of a high-performance granulator is dependent on the careful balance of a number of different factors, making a thorough testing program crucial in the development of a commercial-scale unit.
Granulation drum testing in a facility such as the EMCC Innovation Center provides a valuable opportunity to confirm feasibility of the intended process and develop the data necessary to produce the desired results, among other benefits.
Note: The term “granulation” is used to describe a myriad of processing types. In this case, granulation refers only to wet granulation, also known as agitative, tumble-growth, or non-pressure agglomeration.
WHY GRANULATE IN A DRUM?
Granulation has become an increasingly popular approach to controlling particle characteristics for various types of materials, from specialty and agricultural chemicals, to soil amendments, filter media, and so much more.
Unlike dry granulation methods, wet granulation produces a more spherical granular product. This type of granule has shown to offer several benefits that continue to lend it to premium product markets. Common advantages of this type of granule include:
- Minimal attrition and dust
- Improved flowability
- Better handling and application qualities
- Higher level of control over particle characteristics
- Easy inclusion of beneficial additives
- Greater porosity
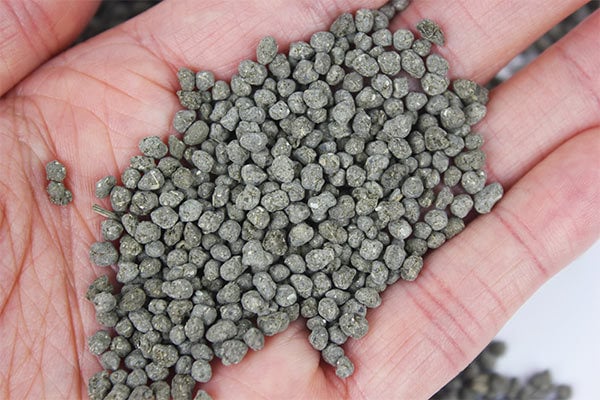
THE VALUE IN TESTING FOR GRANULATION DRUM DESIGN
The straightforward and reliable operation of the granulation drum can be misleading, giving the impression that there is little engineering behind it. On the contrary, the steady operation, minimal oversight, and consistent production of on-spec product are actually the result of a granulator carefully designed by an experienced supplier; in contrast to the smooth operation of a well-designed granulator, a poorly-designed granulator is rife with issues, from an inability to produce on-spec product, to a high rate of process upsets, lost production, and seemingly-endless troubleshooting. Further, not all granulation processes are economically and/or physically viable.
As a result, a thorough testing program should always be the first step in the design of a commercial-scale granulation drum, whether the unit be for a new application, or an existing one. With many interdependent variables, testing serves several purposes that ultimately help engineers to reveal the most optimal granulation drum design for the application at hand:
ASSESSING THE MATERIAL’S UNIQUE RESPONSE TO GRANULATION
The secret behind a well-designed granulator is the understanding that each and every material responds differently to granulation; even the same material from different sources will exhibit variation in behavior. This variability demands that the intended feedstock for a given process be thoroughly evaluated in order to determine whether or not the intended granulation process is feasible, as well as how the granulator can be designed to work best with the unique characteristics of the material source. In some cases, this information may be available through historical data, but in most cases, the data necessary can only be gathered through testing. Raw material characteristics that affect granulation drum design include:
- Particle size distribution
- Bulk density
- Moisture content
- Chemical composition
- Abrasive or corrosive quality
- Temperature (in some cases)
- Ease of granulation
- Special material requirements (heat sensitivity, toxicity, etc.)
Testing will help to identify the parameters necessary for producing the desired granular product from the specific source of material, as well as determine whether or not a preconditioning step will be needed to bring feedstock into a specific range of parameters. Preconditioning is frequently tested as part of granulation in the EMCC Innovation Center.
GATHERING ESSENTIAL PROCESS DATA
Optimal granulation is achieved by using a matrix of process parameters to control granule formation based on the material’s behavior. While many factors play into the success of granulation in a drum, the most influential process data points testing focuses on include:
- Binder and material feed rates
- Percent fill
- Retention time
- Drum speed
- Drum slope
- Spray system design
- Preconditioning requirements
Many of the parameters listed above have a direct effect on the granulation drum size and design, so testing centers around identifying these parameters and determining how they can be leveraged to achieve the desired results.
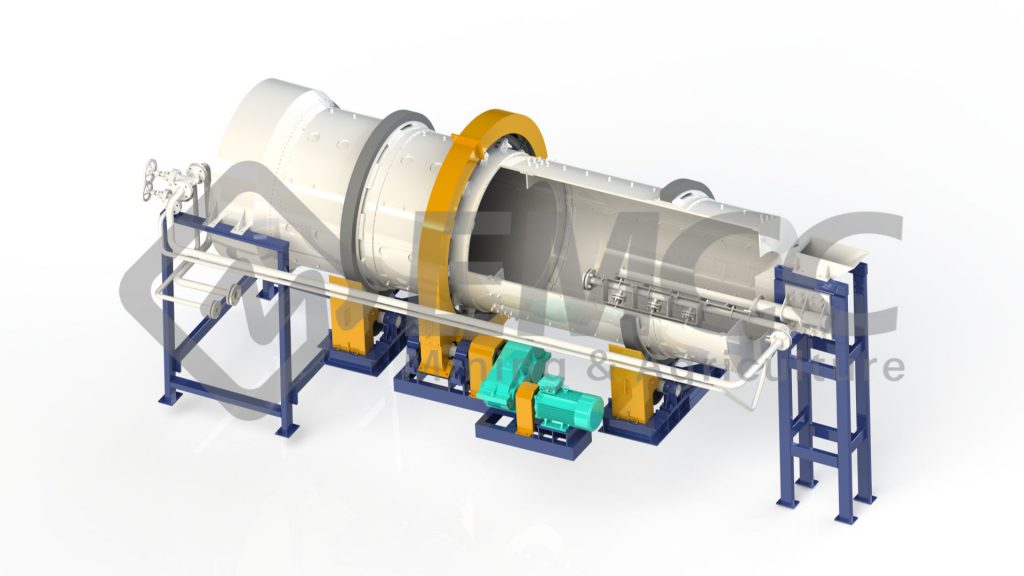
3D Model of a EMCC Granulation Drum
IDENTIFYING POTENTIAL ISSUES & GETTING TO KNOW THE MATERIAL
Materials that are successfully granulated on a batch/bench scale often present unpredictable issues upon scale-up. Pilot-scale testing is therefore used to identify these problems early, reducing the opportunity for surprises later and allowing engineers to adjust the design accordingly before the unit is built.
Similarly, testing builds a valuable familiarity with the material that can expedite future troubleshooting. For example, because testing identifies the specific range in which a material feedstock must fall for any given parameter, operators can be trained in recognizing a problem caused by an abnormality in the feedstock, or in identifying where potential for other problems might exist.
DRYING REQUIREMENTS
Because granulation is a wet process, a drying step is necessary. A variety of industrial dryers are available for reducing the moisture content of granular bulk solids, but the rotary dryer continues to be the preferred approach in most settings.
Rotary dryers are simple to operate, easy to maintain, offer flexibility compared to other dryer types, and have a well-earned reputation for reliability. During testing programs such as those carried out in the EMCC Innovation Center, drying requirements such as retention time, flight pattern, air flow configuration, and more, are determined as part of the process development journey.
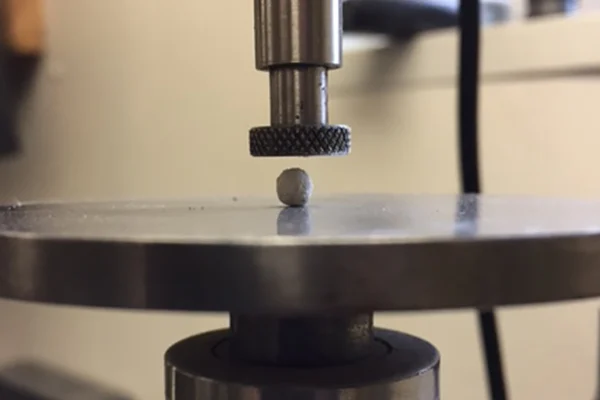
Granule crush strength is tested after granulation and drying in the EMCC Innovation Center
CONCLUSION
The granulation drum is a diverse agitation agglomeration (wet granulation/tumble-growth agglomeration) device applied in an increasing number of applications. As numerous material characteristics and process parameters affect granulation, testing is an essential component in the design of any commercial-scale granulator, not only gathering the necessary material and process data, but also helping to identify potential issues prior to scale-up.
EMCC is the world’s leading provider of granulation drums. Each granulator is designed around the specific requirements of the material and application at hand. Data gathered during testing in the Innovation Center is used to engineer and fabricate a commercial-scale granulation drum uniquely suited for optimal, consistent, and reliable performance. For more information on our granulation drums or testing programs, contact us today!
WE NOT ONLY PROVIDE RELIABLE PRODUCTS, BUT MORE IMPORTANTLY WE PROVIDE RELIABLE PROCESS DESIGN AND EXPERIMENTATION
Rotary Drum Granulator Frequently Asked Questions (FAQs)
Rotary drum granulators, also known as agglomeration or granulation drums, are pivotal to a wide array of industrial processes, helping producers working with bulk solids to condition and agglomerate their materials for downstream processing, easier handling, and improved performance.
In selecting agglomeration/granulation equipment and evaluating the fit of a drum granulator for a given process, many questions may arise. What follows are some of the most frequently asked questions we field in the process of helping our customers bring their granulation processes to life.
HOW DOES A ROTARY DRUM GRANULATOR WORK?
A drum granulator works by tumbling material in the presence of a liquid binder to encourage granule formation and growth. Feed material and binder are constantly fed through the rotating drum. The rolling action, combined with the stickiness from the binder, causes fines to collect together into particles. These particles continue to pick up additional fines and binder as they tumble in the bed, causing them to densify and pick up additional layers in a phenomenon known as coalescence. Tumbling flights can be incorporated into the unit to increase agitation of the material bed.
This way of forming agglomerates is a type of agitation agglomeration also known as wet granulation, balling, or pelletizing.
WHAT TYPES OF MATERIALS CAN A ROTARY DRUM GRANULATOR PROCESS?
Generally speaking, drum granulators can process any bulk solid in the form of a dry, fine powder. This flexibility lends well to a host of industries, processing materials ranging from specialty chemicals and fertilizers, to minerals and ores, and everything in between.
In some cases, the feedstock may require pretreatment in the form of crushing, grinding, or drying to be a suitable feed for the granulator and produce the characteristics desired in the end product.
WHAT’S THE ADVANTAGE OF A ROTARY DRUM GRANULATOR OVER A DISC PELLETIZER?
In choosing between a drum granulator and a disc pelletizer, the drum is often chosen because it offers a higher throughput than the disc pelletizer. The rotary drum also has the advantage of being a “closed” system, meaning that granulation occurs inside a contained environment, so fugitive material is limited.
WHAT CAPACITIES CAN A GRANULATION DRUM ACCOMMODATE?
Granulation drums can be customized to nearly any size, accommodating capacities ranging from 500 lb/hr – 3500 TPH+.
ARE DRUM GRANULATORS BATCH OR CONTINUOUS?
Rotary drum granulators are typically employed in a continuous setting, though they may function as a batch device in some R&D environments, such as the EMCC Innovation Center.
WHAT IS THE RETENTION TIME OF A ROTARY DRUM GRANULATOR?
Retention time is one process parameter used to control the characteristics and quality of the material exiting the drum, so it can vary significantly depending on the process and product goals. In general, retention time in a granulator may fall anywhere between 30 seconds and 60 minutes.
WHAT ARE THE TYPICAL WEAR ITEMS?
Rotary drum granulators are generally low maintenance, but some items can become worn, depending on the operating conditions, and particularly if the drum falls out of alignment. The most common wear items for a drum granulator typically include the liner (where applicable), tumbling flights (where applicable), and potentially trunnion wheels, tires, and thrust rollers.
Rotary drum alignment is an important aspect of drum maintenance to prevent wear of the tires and trunnion wheels. When a drum falls out of alignment, it puts added stress on all components, encouraging undue wear.
DOES THE PRODUCT EXITING THE GRANULATOR REQUIRE DRYING?
Since the granulation process relies on a liquid binder to form and layer granules, the product exiting the granulator is wet and must be dried unless it is moving immediately to a downstream process that does not require drying (such as in the case of iron ore balling, where pellets go to a grate kiln).
Drying is typically carried out in a rotary dryer, which further rounds and “polishes” the granules as a result of the tumbling action that occurs as the drum rotates.
HOW DO I KNOW IF A ROTARY DRUM GRANULATOR IS RIGHT FOR MY APPLICATION?
Whether or not a rotary drum granulator is the right fit for a given project depends on specific process and product goals, such as capacity, level of control over particle characteristics, product parameters, and more.
When it is not clear if a drum granulator will be able to meet the project objectives, testing can be carried out in the EMCC Innovation Center to evaluate the process and identify the most suitable equipment configuration.
IS ANY OTHER EQUIPMENT REQUIRED TO SUPPORT A ROTARY DRUM GRANULATOR?
Drum granulators require a feeding and offtake system to convey material into and away from the drum. They also typically require screens and a recycle circuit to recover overs and unders and recycle them back into the process
Drum granulators are also typically followed by a rotary dryer and in some cases, may be preceded by a mixer for providing a homogeneous feedstock to the unit.
WHAT DOES THE DESIGN PROCESS LOOK LIKE?
Rotary drum granulator design typically begins with testing to assess the feasibility of granulating the intended material and to gather key process data such as percent fill, retention time, drum speed and slope, spray system design, and more.
Once the data has been gathered, engineers work off of this to size the drum and incorporate any necessary features or modifications needed to produce the desired product at the intended capacity.
WHAT DATA IS NEEDED TO DESIGN A ROTARY DRUM GRANULATOR?
A variety of data points are necessary to design the granulator. Along with a process description, the follow data is typically required:
Raw Feed Data
- Material and chemical composition
- Moisture content
- Temperature
- Bulk density and true density
- Material consistency (sticky, plastic, etc.)
- Material qualities (abrasive, heat sensitive, hazardous, etc.)
Product Data
- Desired particle size distribution (PSD – minimum and maximum)
- Expected bulk density
- Binder use and restrictions
Process/Equipment Data
- Preferred materials of construction
- Electrical controls (volts, hertz, phases)
- Temperature of ambient air in processing environemnt – minimum and maximum
- Humidity of ambient air in processing environment – minimum and maximum
- Elevation of plant
- Retention time (if known)
Depending on how much is known about the material, much of this data is often gathered through testing.
WHAT MATERIALS OF CONSTRUCTION ARE AVAILABLE?
Rotary drum granulators can be constructed from nearly any form of steel desired. Carbon steel is typical, as is stainless steel and abrasion-resistant steel.
Depending on the application, various liners are also available for protecting against corrosion and helping to reduce buildup in the drum.
CAN THE GRANULATOR BE AUTOMATED?
Yes. Rotary drum granulators can be fitted with programmable logic controllers (PLCs) and motor control centers (MCCs) for automating the unit, adjusting the process from a human-machine interface (HMI), as well as collecting and trending valuable process data.
ARE DRUM GRANULATORS CUSTOMIZABLE?
Yes. Rotary drum granulators offer ample opportunity for customization. EMCC tailors the mechanical components, internals, materials of construction, size, and more to optimize how the unit works with the material to produce the desired results efficiently.
A variety of add-ons and customizations are available as well, including knockers, liners, spray systems, and more.
WILL THE PROCESS REQUIRE A RECYCLE CIRCUIT?
While some processes don’t necessarily require a recycle circuit, the addition of one is always recommended, as it helps to make the process more efficient.
In other cases, a recycle circuit is necessary for the operation to function on a continuous basis, relying on recycled fines to bring down the moisture content of the feedstock entering the process (a processing technique known as back mixing).
CONCLUSION
Rotary drum granulators provide a reliable, high-capacity processing device for conditioning and granulating bulk solids in a range of settings.
EMCC granulators are expertly engineered to suit the specific processing objectives at hand, and can be provided as a standalone unit or as part of a complete granulation line. In addition to the world’s most reputable granulators, EMCC also provides feasibility and process development services, as well as parts and service support. For more information on our granulation drums, contact us today!
WHY CHOOSE EMCC AS YOUR PARTNER?
Shanghai Exceed Industry Co., Ltd (China EMCC) is a manufacturing enterprise specializing in high-tech fertilizer machinery. For many years, we have devoted to producing inorganic and organic fertilizers granulator equipments. By consistently creating values for our customers around the world, we have become one of the leading suppliers in global agricultural fertilizers industry. With China EMCC, you may get comprehensive services of consulting, design, equipment, installation, training, emergency assistance, field assistance, spare parts and routine maintenance to save fertilizer plants cost.
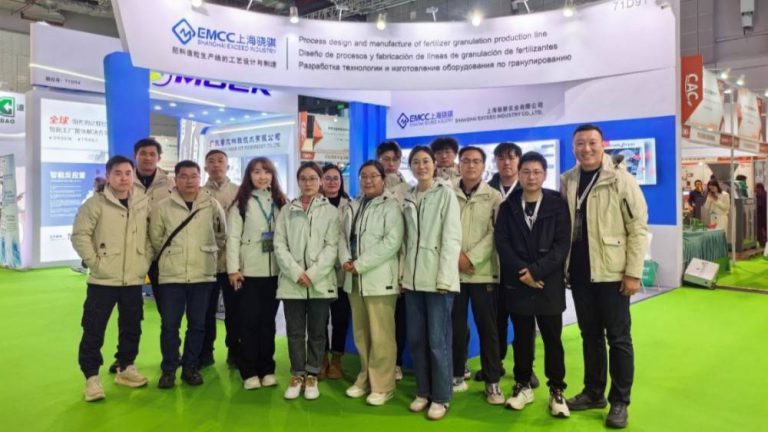
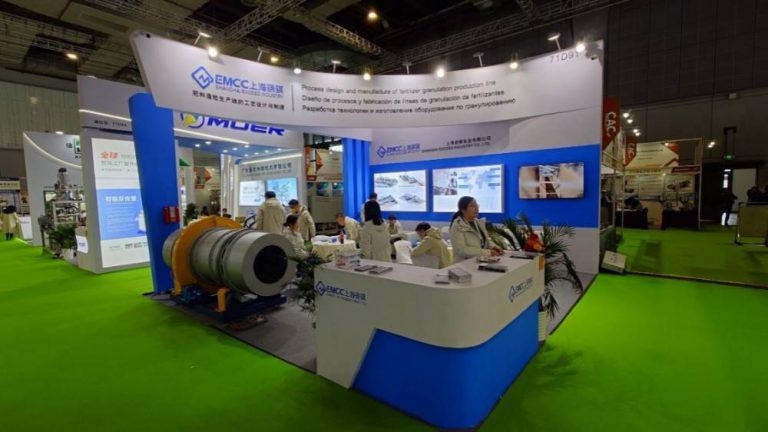
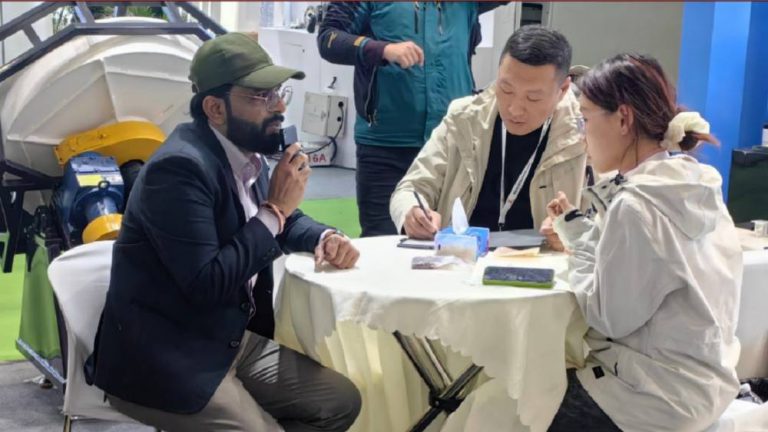
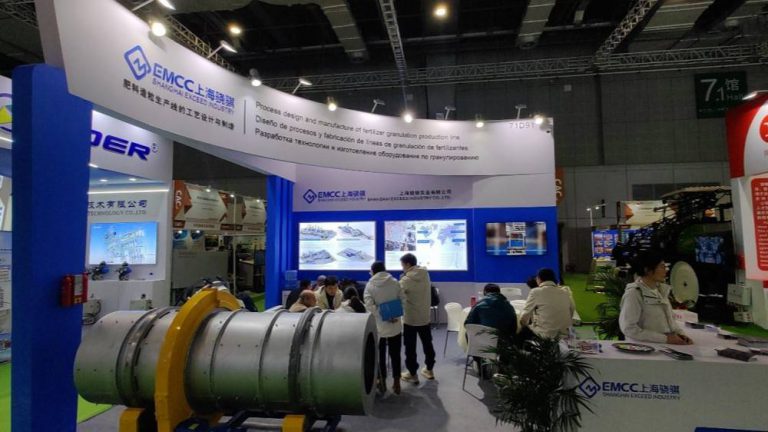
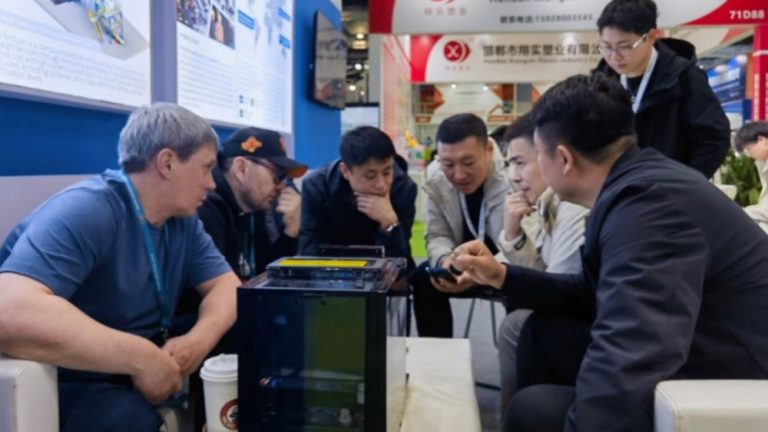
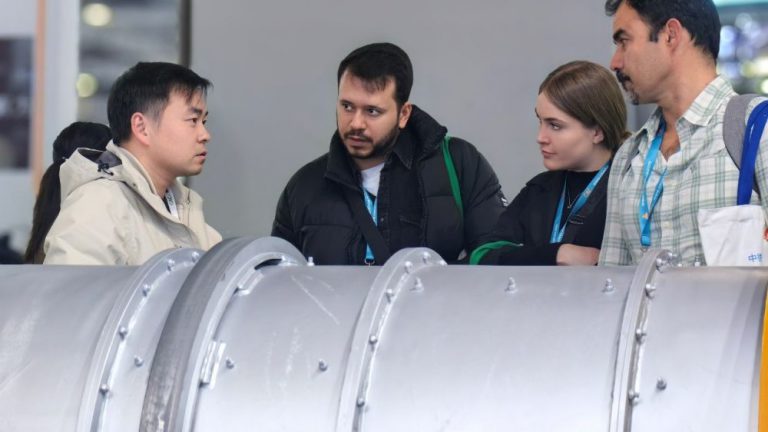
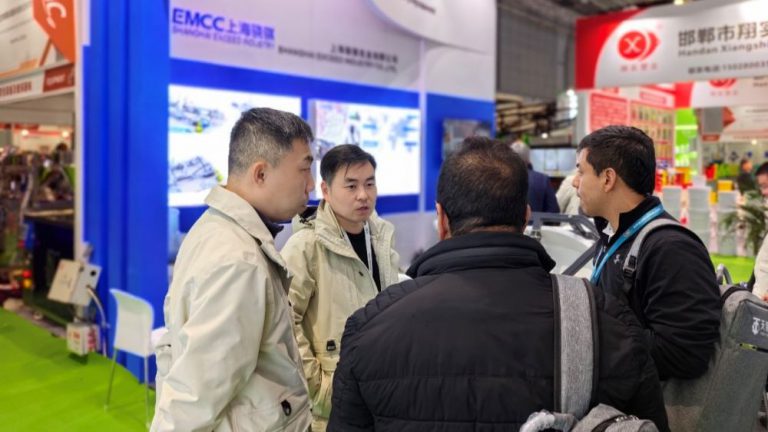
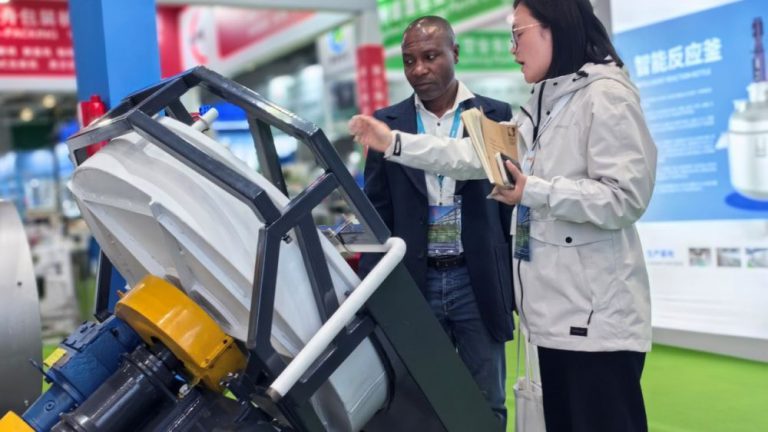
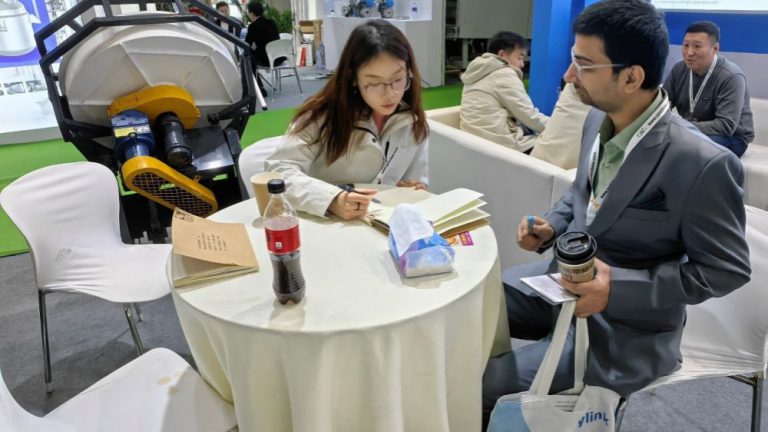
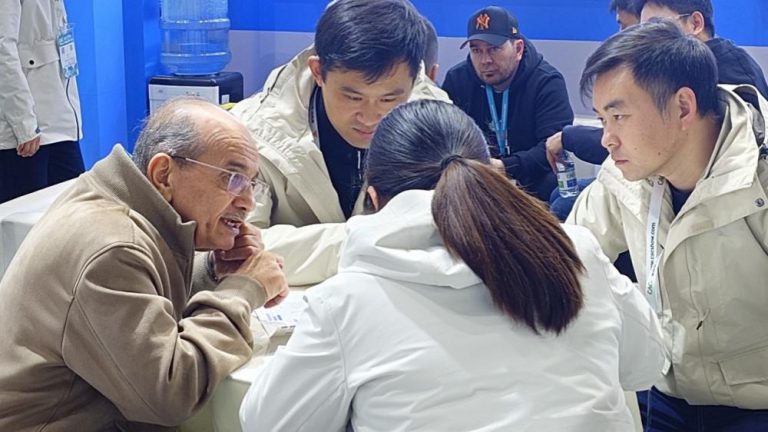
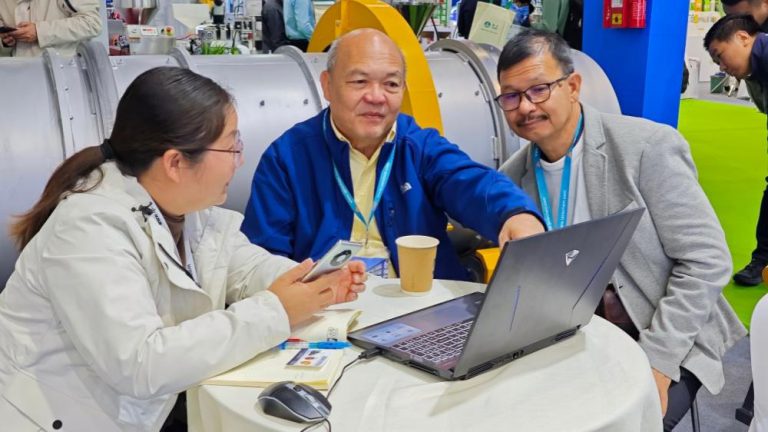